Compared with the original simulator, the new simulator has been greatly improved in the following aspects: First, in the aspect of heat conduction, automatic temperature control is realized to ensure that the temperature in the kettle is consistent when the temperature is high and the temperature is constant. The simulation sample is consistent with the evolution of its products. Secondly, in terms of temperature control, by using the external temperature control and the internal temperature control method, the over-temperature phenomenon that may exist in the original instrument is completely avoided. The third is to reform the vacuum pump circuit. The automatic conversion between vacuuming and nitrogen filling is realized, and the operation is more convenient.
According to reports, the hot rock simulation test of source rock has been widely used in oil and gas exploration, especially in the study of organic matter evolution characteristics, oil and gas source comparison, source recourse and hydrocarbon generation mechanism and hydrocarbon migration. The use of hot-pressure simulation of source rock has given it unique results and rich information.
The successful development of the new conventional hot-pressure simulation tester is not only conducive to the popularization and application of this test method, but also because the simulation tester has the characteristics of accurately collecting and calculating the carbon number of liquid hydrocarbons from 6 to 14 fractions. It is of great theoretical significance to understand the hydrocarbon generation pattern of source rocks and to understand the geochemical change law of this fraction and the quantitative evaluation of the oil layer.
Metals, alloys and composite powders commonly used in thermal spray hardfacing technology and coating service. These unique powders are instantly heated by thermal spraying (welding) methods such as high temperature flame or explosive flame, and are sprayed and deposited on the cold or hot workpiece surface with high-speed heat flow in a molten or semi-melted state to form a surface Reinforcing layer, in order to improve the wear resistance, corrosion resistance, heat resistance, oxidation resistance or repair of external dimensions of the workpiece surface. XTC produces WC, CrC, Oxide Ceramic, Boride Powder, Metal Alloy Powder, Pure Metal and Spray Wire, etc. product. For HVOF/HVAF/plasma/Flame spray coating and applications. Meet the wear and corrosion resistance requirements of different surfaces.
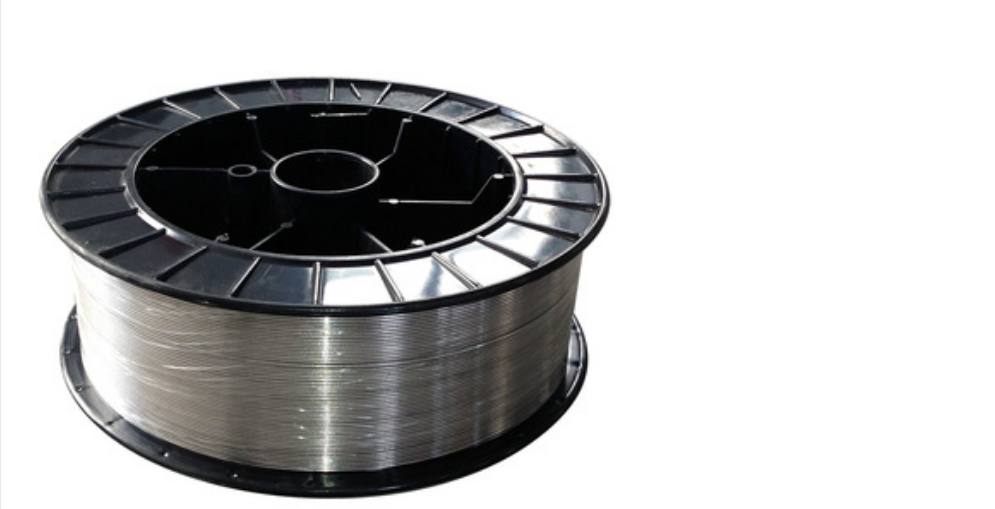
WC, CrC oxide ceramic powder and boride products are excellent in wear resistance and high temperature corrosion resistance. Taking WC products as an example, the hardness can reach HV1300-1500, and the temperature of CrC products can reach 800 degrees Celsius.
Metal alloy powder, Pure Metal and Spray Wire products have more applications in glass mold, steel and machinery industries. And XTC products are now become more and more popular in Metal spray coating and thermal spray coating industry.
Coating Service,Metal Spray Coating,Flame Spray Coating,Thermal Spray Coating
Luoyang Golden Egret Geotools Co., Ltd , https://www.xtcwelding.com