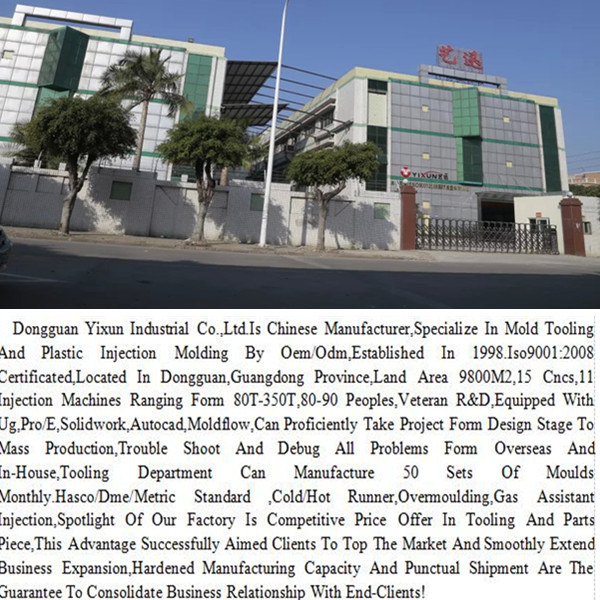
Professional plastic mold
Mold or die are the common terms used to describe the tool used to produce plastic parts in molding.
Since molds have been expensive to manufacture, they were usually only used in mass production where thousands of parts were being produced. Typical molds are constructed from hardened steel, pre-hardened steel, aluminum, and/or beryllium-copper alloy.
Injection molding consists of high pressure injection of the raw material into a mold which shapes the polymer ( plastic) into the desired shape
Material for the part is fed into a heated barrel, mixed, and forced into a mould cavity, where it cools and hardens to the configuration of the cavity. After a product is designed, usually by an industrial designer or an engineer, moulds are made by a mouldmaker (or toolmaker) from metal, usually either steel or aluminum, and precision-machined to form the features of the desired part. Injection moulding is widely used for manufacturing a variety of parts, from the smallest components to entire body panels of cars
Injection molding is used to create many things such as wire spools, packaging, bottle caps, automotive dashboards, Game boys, pocket combs, some musical instruments (and parts of them), one-piece chairs and small tables, storage containers, mechanical parts (including gears), and most other plastic products available today. Injection molding is the most common modern method of manufacturing parts; it is ideal for producing high volumes of the same object.
2.Mold information
Â
Shaping Mode | Plastic Injection Mould |
Application: Industry | Auto ,  Medical.   Home appliance, Daily Community,  Telecommunication |
Service area | Transparent, Over mold, double color, air assistant forming, deep barrel, Design R&D, Assembly |
Production Equipment | Elite Plastic Injection Machines ,CNC, Mirror EDM machine, Wire Cutting machine, Carving machine, Lathe Drilling machine, Grinding machine, Milling machine, |
QC Machine | 3D Measurement, Profile Projector, Hardness Tester and other regular size inspection equipment. |
Mold Cavity: | Single or Multi-Cavities Available |
Runner System: | Cold or Hot-Runner Available |
Mould Base | LKM, HASCO, DME etc |
Mould Material: | P20, 738, 738H, 718, 718H, NAK80, S136, S136H, 2378H, 2311, 2083, 2316, H13, SKD61, 2344, 8407 And other material as requirement |
Hardness of steel | Vacuum quenching ,Nitride, HRC41-47, HRC46-50,HRC60 |
Plastic Material: | ABS, PP,PC, POM ,PVC, PE, PET, PMMA , Acrylic, and other material As requirement |
Mold Lead time: | 4Weeks T1 samples , exact time depends on Mould Complexity |
Mould Life: | 0.3 Million Shots- 1Million shots |
Packing: | Exporting standard |
3.Mold manufacturing show and mold management flow
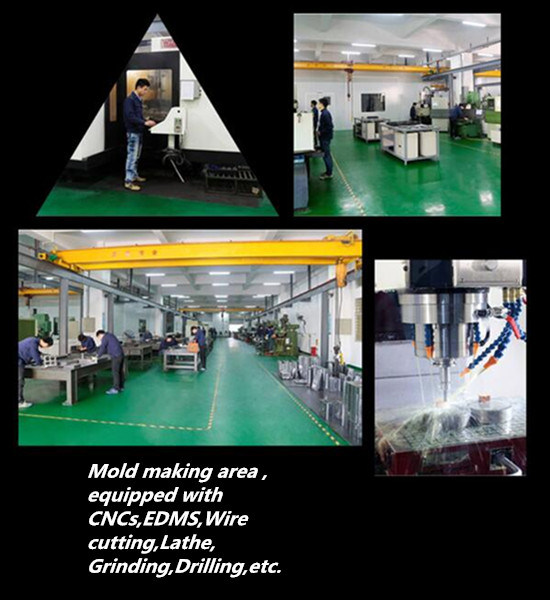
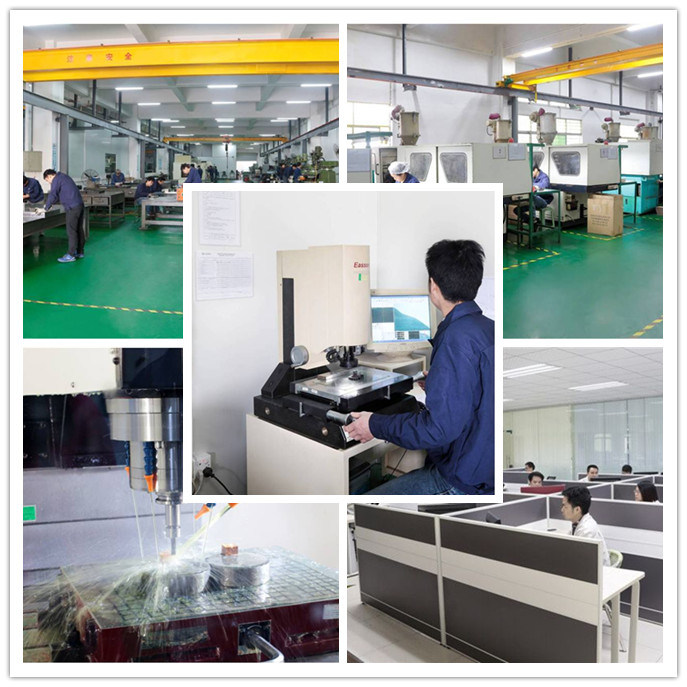
4. Mold inquiry :
If you are going to make an inquiry of mold, please give basic information with 3D drawing or 2D drawing or any other detail information (material, part weight, qty, etc), we will give you answer within 24hours in working day.
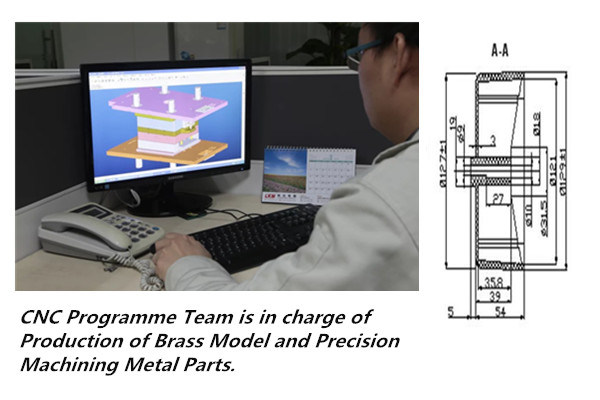
Project management flow
Business Step | |
1.R&D | We support customer R&D. Make the files or improve the design if you needed |
↓↓↓ | |
2.Quotation Making | Mould Quotation will be finished in 1 day according to information we get |
↓↓↓ | |
3.Negotiation | The quality ,price ,material, delivery time .payment item. ect |
↓↓↓ | |
4.Mould Design | 3-5Â days for mould and product 3D/2D drawing design |
↓↓↓ | |
5.Mould | According to customers' request to build the mould.Before make the mould .we send mould design to customer approval first . Mould will be usually finished in 25-60 days |
↓↓↓ | |
6.Mould Testing | When moulds are finished,we will test the moulds to check it satified consumers' needs.And we will send samples for consumers' reference. |
↓↓↓ | |
7.Sample confirm | If the first sample come out is not satisfied customer .we modify the mould and until meet customers satisfactory |
↓↓↓ | |
8.Delivery | Delivery goods by sea or by air ,according customers requirement |
5. Usual question and answer
Q: What do you (DONGGUAN YIXUN INDUSTRIAL CO.,LTD) do
A: We do plastic mold and injection molding........
Q:: What's your( DONGGUAN YIXUN INDUSTRIAL CO.,LTD)Â advantages
A:: We have 20 years professional experience and team in plastic injection molding and mould
Our quality is fine., We get ISO certificate and TS16949 certificate
Our delivery is always in time
Good service
Q:: What industry do your (DONGGUAN YIXUN INDUSTRIAL CO.,LTD) business cover in the last 20years
A:: main Auto, medicals, appliances, daily commodity, electronics and telecommunication and other industry which plastic products.
Q: What software do you (DONGGUAN YIXUN INDUSTRIAL CO.,LTD)use and what format can you open
A: AutoCAD, Pro/E, UG, SolidWorks, format, x-t, step, igs ,dwg etc.
Q:Â How about your design ?
A: Design mould is our strong advantages as we have design team. We can also design plastic proudct for customer which need require description clearly from customer
Q: Did you design product successfully ?
A: Yes, I designed successfully for some of our customer
........
Please make sure to contact us with plastic part's basic information (which is very very important) when you are going to make inquiry of mold. Thanks.
Wish all buyers can find satisfying supplier in China!
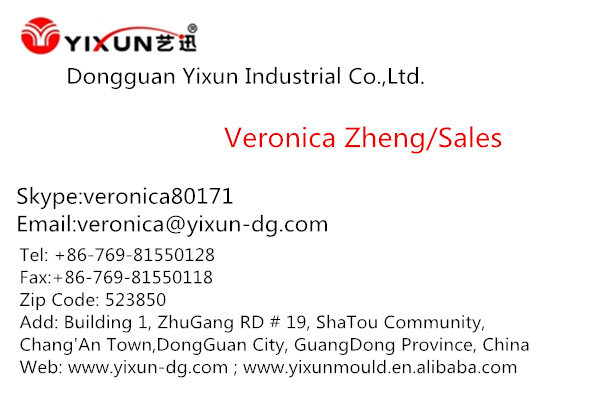
Â
Ethylene Cracking Furnace Anchor
Anchors are mostly used as fixtures for integral linings (castable, plastic and sprayable linings). Refractory brick linings also use anchors, but they are not used in many occasions. Metal anchors are usually used to support and fix thin or heat-insulating integral linings, such as chimney linings, wear-resistant linings of petrochemical catalytic cracking reactors (usually tortoise shell mesh anchors), integral jet metallurgy The lining of the spray gun, the overall lining of the immersion pipe of the DH and RH vacuum degassing devices, the lining of the rotary kiln discharge day, the feeding port, etc. Metal anchors are mostly used to fix linings with a long-term use temperature below 1200 °C, or short-term use temperature above 1200 °C that can be used intermittently. Ceramic anchors are usually used to fix thicker (greater than 200mm) integral linings and are characterized by:
(1) It can withstand higher operating temperatures, and is generally used in the lining of kilns that are used for a long time above 1200 °C;
(2) It can withstand the erosion and corrosion of corrosive atmosphere;
(3) It can be extended to the working surface to reduce the peeling of the overall lining;
(4) Compared with metal anchors, the contact area with the refractory lining is large, so it has a greater supporting capacity;
(5) The thermal expansion coefficient is equivalent to that of the overall refractory material, which can eliminate the cracking or peeling of the lining due to thermal expansion mismatch
Ethylene Cracking Furnace Anchor,Corbel Anchor,601 Inconel Refractory Anchor,310 Stainless Steel Refractory Anchor
Puyu kiln technology (jiangsu) CO.,LTD , https://www.anchorpy.com