- Model NO.: YX65-400
- Condition: New
- Application: Machinery & Hardware
- Automatic Grade: Automatic
- Control System: PLC Frequency Control System with Touch Screen
- Usage: Production of Roof Panel
- Weight: 7000kgs
- Trademark: RUIYU
- Origin: Xiamen, China
- Certification: CE
- Customized: Customized
- Power Source: Electric
- Product Type: Roll Forming Machine
- Raw Materia: Gi, PPGI, Al...
- Motor Power: 7.5kw*2 Sets
- Voltage: 380V/50Hz/3pH
- Specification: 5800*1700*1500mm
- HS Code: 84552210
1.Processing Flow Diagram of Roofing Roll Forming Machine
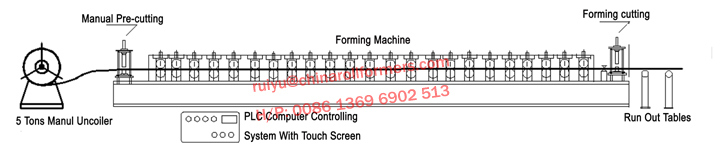
2.Product Description
Main Technic Parameter:
 Size |  5800*1700*1500mm |
 Weight |  7000KGS |
 Voltage |  380V/50HZ/3PH |
 Motor Power |  7.5KW*2 sets |
 Hydraulic Power |  2.2KW |
 Forming Steps |  13 |
 Working Speed |  8-14m/min |
 Height of Roofing |  65mm |
 Effective Width |  400mm,425mm |
 Feeding Material Width |  575-578mm,600-603mm |
 Thickness for Aluminum Sheet |  0.8-1.2mm |
 Thickness for Steel |  0.6-1.0mm |
 Min. Width of tapered roofing |  250mm |
 Min.Length of tapered roofing |  1000mm |
 Cutting,Forming Tolerance |  ±2mm |
 Roller material |
 High grade 45# forged steel, Plated hard chrome  and polished all the rollers   |
 Material of shaft |  High grade 45# forged steel |
 Sprocket wheel |  45 steel high-frequencies quench |
 Cut-off system |  Hydraulic cutting device |
 Material for Blade |  Cr12 mold steel with quenched treatment 60-62°C |
 Material for frame of machine |  Fine welded structural steel; |
 Material for producing roofing |  Aluminum Sheet,PPGI Steel and G.I. Steel |
 Painted Color |  Customization |
Main Accessories:
(1) Main Forming Machine for making Straigt and Tapered Standing Seam Roofing; |
(2) 5 Tons*600mm Uncoiler ; |
(3)Â Leveler closed to feeding position (7 Rollers); |
(4) Hydraulic System; |
(5) PLC Computer Controlling System With Touch Screen ( Brand:Schneider ); |
(6)Â Hydraulic Forming Cutter(2 sets cutters,one set for YX65-400,one set for YX65-425); |
(7)Â Device for making tapered standing seam roofing; |
(8) Safety Cover; |
(9) Auto Seamer (2 set, Voltage: 220V/50HZ/1PH, 3 Steps for seaming straight roofing sheet); |
(10)Â Hand Seamer(3Â PCS); |
(11)Â Run out tables(3Â PCS); |
(12)Â Tools; |
(13)Â Operation Manual. |

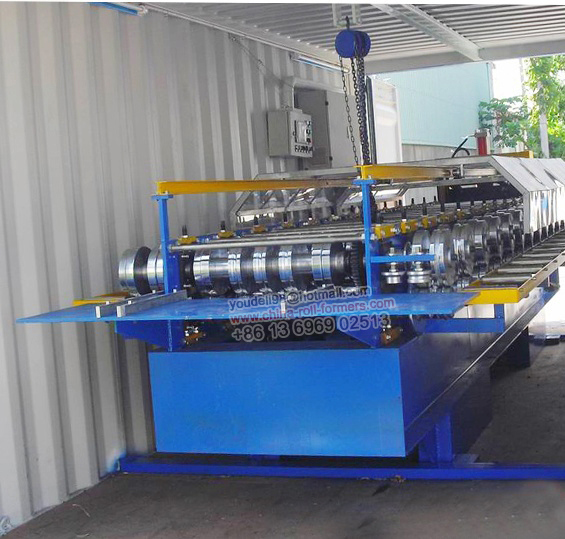
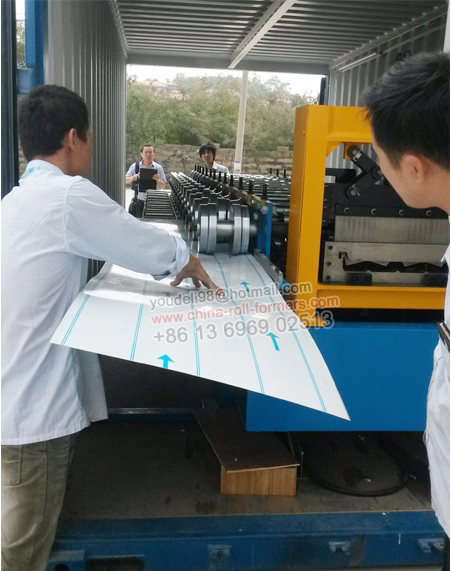
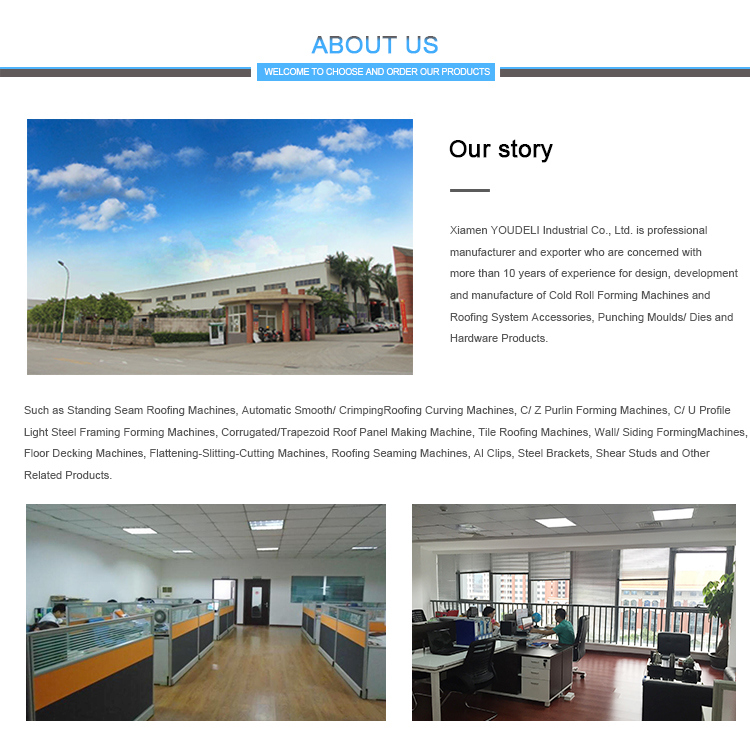
Â
Aluminum extruded finned tubes using the form of the base tube covered with aluminum tube(the base tube can be carbon steel, stainless steel, copper) through machine extrusion, forming a tube fin, the fin base and the tube outer wall is close fitting, this fin tubing control can make finned tubes with high heat transfer coefficient and heat transfer performance.
Aluminum extruded finned tubes, also called [integral finned tubes" using the form of the base tube covered with aluminum tube(the base tube can be carbon steel, stainless steel, copper) through machine extrusion, forming a tube fin, the fin base and the tube outer wall is close fitting, this fin tubing control can make finned tubes with high heat transfer coefficient and heat transfer performance. Extruded finned tube can be made of iron, copper or aluminum tube by compound rolling, which has the advantages of tight bonding, small thermal resistance, good heat transfer performance, high strength, small flow loss, strong anti-corrosion performance, not easy to deformation under long-term hot and cold working conditions, long working life and so on.
Extruded finned tube manufacturing process
Pipe line--compressing or rolling--strip peeling--washing--pressure test--blast blowing--packaging.
The extruded fin tube is formed by a bimetallic tube consisting of an aluminum outer tube and an inner tube of almost any material. The fin is formed by rolling the material from the outside of the outer tube to provide an integrated fin with excellent heat transfer performance and life. The extruded fins provide excellent corrosion protection for the base tube.
The production method of the composite finned tube mainly includes the extrusion method: the bimetallic composite tube is lined with a mandrel, and driven by the rotation of the roller blade, the composite tube is processed on the outer surface through the cavity formed by the rolling groove and the core head Out fins. The heat transfer tube produced by this method is an organic whole with its outer tube and fins, so there is no problem of contact heat loss, and it has good performance and high heat transfer efficiency.
Extruded finned tube advantage
Compared with the ordinary wound finned tube, the contact thermal resistance remains stable in a large range with the temperature change, so the heat transfer performance of the bimetallic aluminum extruded finned tube is better than the spiral fin tube in the limit tube wall temperature range.
In addition, compared with the coiled tube, the bimetallic aluminum extruded fin tube has outstanding corrosion resistance and high strength, it can withstand 4.0MPa water pressure cleaning, the fins still do not fall down, the base of the bimetallic aluminum extruded tube. The tube can be selected according to the corrosion of the fluid in the tube and the processing technology. The base tube can be carbon steel, copper, stainless steel, etc.
Extruded finned tube applications
Extruded finned tubes are the main equipment for air coolers and are commonly used as heat exchangers in power plants (electric, nuclear, thermal and geothermal). Steam condensate system. Chemical and petrochemical industries. Food processing plants and refrigeration technology. Industry (steel mills, incinerators, gas compression facilities). Petrochemical, power plant and power plant renovation, air conditioning and refrigeration, boilers, finned tube economizers and air preheaters. Maximum working temperature is 280°C-300°C.
Extruded Finned Tube,Extruded Bimetallic Fin Tube,Aluminum Extruded Finned Tube,Heat Exchanger Extruded Fin Tube
Murphy Thermal Energy Co., Ltd. , https://www.murphyfinnedtube.com