First, the principle of critical emergency trip protection control system Jiangsu Ligang Electric Power Co., Ltd. Phase 2 2 × 350MW coal-fired unit original small machine control system consists of a local control cabinet, a monitoring instrument TSl cabinet, a J17 relay cabinet and One-sided process control DPU cabinet configuration. The local control cabinet consists of 20 process signal relays, 1 "trip/reset" relay and 15 pressure switches. Each small aircraft is equipped with a set of critical trip protection system. When the operating parameters reach the set value, a trip signal is issued. The small machine discharges the security oil and anti-fuel oil, and closes the high and low pressure main valves and the high and low pressure regulating doors. Small trip. In addition, the “Break†button is provided on the central control room BTG tray and the small machine local cabinet.
Small machine original trip solenoid valve electrical schematic diagram shown in Figure 1. When any trip condition occurs, the trip relay 86T is energized, the normally closed contact is opened, the tripping solenoid valve SV1, SV2 is de-energized, the security oil and the anti-fuel oil are drained, and the small machine trips. Trip conditions are as follows.
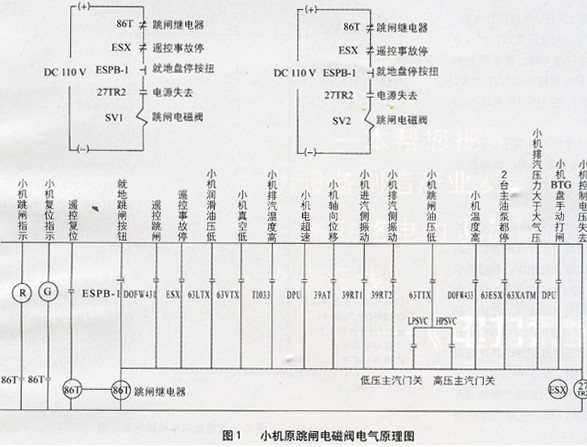
a. Manual control room BTG disk manual trip (ESX).
b. Small Machine Manual Trip (ESPB-1)
c. small electrical speeding (DPU).
d. Small bearing lubrication oil pressure (63LTX) (delayed 3s).
e. Small machine exhaust port vacuum low (63VTX) or exhaust pressure is higher than atmospheric pressure (63XATM).
f. Small exhaust steam temperature (TI033).
g. small axial displacement (39AT).
h. Small inlet side and exhaust side bearings have high vibration (39RTl, 39RT2).
i. Small machine security oil pressure, and high and low pressure main valve is not fully closed (63TTX).
j. Small main pump stop (63ESX (delay 35).
k. Small machine local trip relay control circuit loses power (27TR2L.
l. The contact DOFW431 is closed. It is the trip signal sent from the 11th DPU cabinet to the floor cabinet. The signal includes the following contents: the front pump is stopped; the exhaust valve is not fully open; the main pump thrust bearing and the drive end High bearing and non-drive end bearing temperature; main pump seal water flow low, delay 30s.
m. The contact DOFW433 is closed. It is the trip signal sent from the 18th DPU cabinet to the floor cabinet. The signal includes the following contents: The bearing temperature of the inlet side or exhaust side of the small machine is high; the thrust bearing face of the small machine or not Working face temperature is high.
When there is no above-mentioned tripping condition, press the "reset" button of the central control room BTG disk to energize the relay 86T, so that the solenoid valves SV1 and SV2 are energized. Then press the "reset" button on the local cabinet to enable the two "reset" solenoid valves to be energized to establish the security oil pressure and reset the small machine.
Second, the reasons for the transformation of the small machine control system The operation of the second phase of the small machine has been running well for the past eight years, but the design of the control system is inadequate.
a. All the protection tripping signals of the small machine are mostly realized by hard-wired loops. In addition to the signals contained in DOFW431 and DOFW433 and the "electric overspeed" protection signal can be enforced, the rest of the trip signals can not be removed by force. The thermal control personnel can only use the disconnection or short circuit in the local control cabinet. Unprotection can easily cause grounding, short circuit, and control systems. In order to avoid misoperation, it was necessary to stop handling the small aircraft before handling it, but the outage of the small aircraft would cause economic losses.
b. The collection of the trip protection signal of the small machine is not standardized. Some local switches are directly connected to the protection circuit, and some of them are switched into the trip protection circuit after the local relay is converted, and some are connected to the protection circuit after the TSI cabinet or DPU cabinet is switched over by the small machine, and the wiring of the local control cabinet is rather confusing. In case of a failure of the control loop of the small machine, cumbersome, messy and extremely non-standard control loops bring great inconvenience to fault judgment and processing, and increase the risk of handling faults.
c. The electrical components such as the relays and buttons in the local control loop are energized at high temperatures all the year round. They have gradually become old and their reliability has been declining year by year. This has brought certain hidden dangers to the safety of the small aircraft.
d. The small steam turbine exhaust butterfly valve does not open to the position and causes the small turbine to trip. This protection logic is unreasonable. Even if the butterfly valve is closed, there is high exhaust pressure and high exhaust temperature protection. This protection once mistakenly skipped the small aircraft and caused Class II obstacles. Therefore, this protection can be considered cancelled and replaced by an alarm signal.
Third, small machine protection tripping system transformation program with reference to other DCS control system, the traditional hard-wired logic into soft logic is a safe and economical program. The logic behind the transformation is basically the same as the original logic, but the new control system strives to be simple, clear, and intuitive. Based on this idea, all the electrical components of the floor cabinets were removed, the local input signals were directly sent to the WDPF cabinet, and the configuration was changed and protected with DPU soft logic.
3.1 Modification of the local cabinet a. Remove the following components on the local cabinet: High oil level, low alarm, small unit reset, small unit tripping, allowable main valve test, normal high/low pressure main valve test ; Exhaust steam temperature and speed 2 meter; oil level meter test, emergency stop, high pressure main valve and low pressure main valve test 4 buttons; all intermediate relays in the cabinet. The mechanical overspeed trip reset button and six pressure gauges are still left on the floor cabinet, and the mechanical overspeed trip reset button contact signal is sent to the No. 18 DPU.
b. Replace and rearrange the local cabinet terminals.
c. Replace the signal cable from the local device to the local cabinet and the local cabinet to the DCS and TSl cabinets.
3.2 The transformation of the power supply The small cabinet DCll0V and AC220V control power supplies are sent from the power distribution center to the local cabinet. After the modification, cancel the DCllOV and AC220V power supplies from the power distribution center to the in-place cabinet, and increase the power distribution center to the centralized control power cabinet. The DCllOV power supply of the 4JSB cabinet is divided into 5 small switches in the power cabinet to be used as small and high voltages. The main valve opens and closes the solenoid valve and the power of the small trip solenoid valve SVl, SV2. In addition, set up four AC220V small switches as the zero speed switch, small high and low pressure hydrophobic 1 door and small reset solenoid valve SV7A, SV7BE6 source.
3.3 Relay contact transformation The contact of J17 relay cabinet internal relay k78 is changed from the normally open contact to the normally closed contact. The BTG disk emergency trip button retains the original hard-wired circuit and implements the trip function. The original BTG disc emergency trip button controls the k78 relay. The k78 relay normally open contact is sent to the local cabinet relay ESX. The trip relay 86T is controlled by the contact of the relay ESX. When the BTG disk emergency trip button is pressed, the contact point on the button is turned on, 28 is charged, and the normally open contact of the k78 relay is closed to make the relay ESX energized. The ESX normally open contact is closed and the trip relay 86T is energized. The solenoid valve SVl, SV2 loses power and small machine A trips. After the transformation, the k98 relay contact directly enters the tripping solenoid valve SVl, SV2 electrical circuit, when the small machine normal operation, the contact is in the on state, so the contact should be changed to the normally closed contact.
3.4 Logic configuration modification a. Figure 2 is the schematic diagram of the transformed small machine trip. The contact DOFW431 is a trip signal composed of all trip signals and sent through the J17 relay cabinet. When the small unit is reset, the signal is set to "1" and the contact is connected. As long as any trip signal is issued, DOFW431 will be set to "0". The relay contact is disconnected and the tripping solenoid valves Sk/l and S1/2 are de-energized. , Leaving security oil and anti-fuel oil. The contact k is the "manual stop" button on the BTG disk control circuit J17 relay box k28
With the contact point, the contact is connected during normal operation. When the "manual stop" button is pressed, the contact is disconnected. The tripping solenoid valve ports SVl and SV2 are de-energized, and the security oil and anti-fuel oil are discharged.
b. The small exhaust steamer valve is not fully protected. The alarm is changed by tripping.
c. Cancel the high/low pressure main valve test control function of on-site cabinet minicomputer, and retain the operator station test function.
d. To cancel the high/low test function of the oil level on the local cabinet, add the high/low alarm on the oil level in the operator station screen.
e. Added a small soft reset function to the operator station.
f. Small machine reset adopts one-button reset, that is, the original BTG disk and local reset to establish trip hydraulic pressure to any reset button to reset can establish trip hydraulic pressure (on-site reset button, BTG disk small hand operator reset Button, operator station soft reset).
g. As all the intermediate relays of the floor cabinet have been removed, the contact originally used by the relay 86T as the reset signal of the small machine and the trip signal no longer exists, and the reset signal and the trip signal are replaced by the security oil pressure signal (63TT) after the modification.
h. In the 18th DPU increase the small machine to reset the Dl point in place.
i. Three screens related to the operator station and the small machine, alarm window prompts, trip condition display, buttons, text, and signal indications are modified accordingly.
Fourth, the transformation effect This transformation eliminates many of the original control system of hidden dangers, and significantly improved the reliability and economic control of the small machine control system.
a. Dismantled all the relays and other electrical components of the local cabinet, and sent the signal directly to the DPU cabinet through the local cabinet, which reduced the intermediate links and made the system more simple and clearer and more intuitive.
b. All signals after transformation can be enforced by point information, and the system is more secure and reliable.
c. The transformation of the power supply system ensures the independence of each user's power supply and ensures the safety and stability of the control system.
d. The modification of the operator station screen allows the operator to see at a glance the operating conditions and the trip conditions of the small machine.
Small machine original trip solenoid valve electrical schematic diagram shown in Figure 1. When any trip condition occurs, the trip relay 86T is energized, the normally closed contact is opened, the tripping solenoid valve SV1, SV2 is de-energized, the security oil and the anti-fuel oil are drained, and the small machine trips. Trip conditions are as follows.
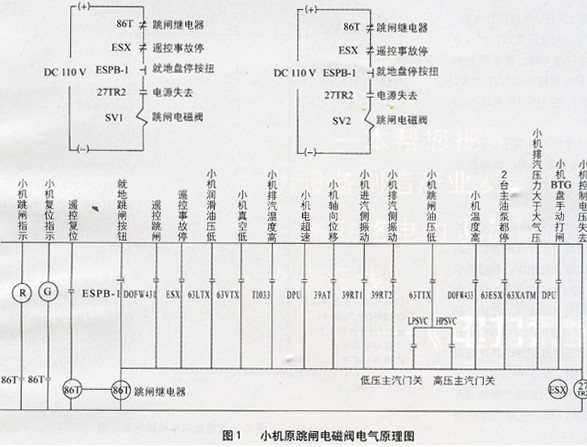
a. Manual control room BTG disk manual trip (ESX).
b. Small Machine Manual Trip (ESPB-1)
c. small electrical speeding (DPU).
d. Small bearing lubrication oil pressure (63LTX) (delayed 3s).
e. Small machine exhaust port vacuum low (63VTX) or exhaust pressure is higher than atmospheric pressure (63XATM).
f. Small exhaust steam temperature (TI033).
g. small axial displacement (39AT).
h. Small inlet side and exhaust side bearings have high vibration (39RTl, 39RT2).
i. Small machine security oil pressure, and high and low pressure main valve is not fully closed (63TTX).
j. Small main pump stop (63ESX (delay 35).
k. Small machine local trip relay control circuit loses power (27TR2L.
l. The contact DOFW431 is closed. It is the trip signal sent from the 11th DPU cabinet to the floor cabinet. The signal includes the following contents: the front pump is stopped; the exhaust valve is not fully open; the main pump thrust bearing and the drive end High bearing and non-drive end bearing temperature; main pump seal water flow low, delay 30s.
m. The contact DOFW433 is closed. It is the trip signal sent from the 18th DPU cabinet to the floor cabinet. The signal includes the following contents: The bearing temperature of the inlet side or exhaust side of the small machine is high; the thrust bearing face of the small machine or not Working face temperature is high.
When there is no above-mentioned tripping condition, press the "reset" button of the central control room BTG disk to energize the relay 86T, so that the solenoid valves SV1 and SV2 are energized. Then press the "reset" button on the local cabinet to enable the two "reset" solenoid valves to be energized to establish the security oil pressure and reset the small machine.
Second, the reasons for the transformation of the small machine control system The operation of the second phase of the small machine has been running well for the past eight years, but the design of the control system is inadequate.
a. All the protection tripping signals of the small machine are mostly realized by hard-wired loops. In addition to the signals contained in DOFW431 and DOFW433 and the "electric overspeed" protection signal can be enforced, the rest of the trip signals can not be removed by force. The thermal control personnel can only use the disconnection or short circuit in the local control cabinet. Unprotection can easily cause grounding, short circuit, and control systems. In order to avoid misoperation, it was necessary to stop handling the small aircraft before handling it, but the outage of the small aircraft would cause economic losses.
b. The collection of the trip protection signal of the small machine is not standardized. Some local switches are directly connected to the protection circuit, and some of them are switched into the trip protection circuit after the local relay is converted, and some are connected to the protection circuit after the TSI cabinet or DPU cabinet is switched over by the small machine, and the wiring of the local control cabinet is rather confusing. In case of a failure of the control loop of the small machine, cumbersome, messy and extremely non-standard control loops bring great inconvenience to fault judgment and processing, and increase the risk of handling faults.
c. The electrical components such as the relays and buttons in the local control loop are energized at high temperatures all the year round. They have gradually become old and their reliability has been declining year by year. This has brought certain hidden dangers to the safety of the small aircraft.
d. The small steam turbine exhaust butterfly valve does not open to the position and causes the small turbine to trip. This protection logic is unreasonable. Even if the butterfly valve is closed, there is high exhaust pressure and high exhaust temperature protection. This protection once mistakenly skipped the small aircraft and caused Class II obstacles. Therefore, this protection can be considered cancelled and replaced by an alarm signal.
Third, small machine protection tripping system transformation program with reference to other DCS control system, the traditional hard-wired logic into soft logic is a safe and economical program. The logic behind the transformation is basically the same as the original logic, but the new control system strives to be simple, clear, and intuitive. Based on this idea, all the electrical components of the floor cabinets were removed, the local input signals were directly sent to the WDPF cabinet, and the configuration was changed and protected with DPU soft logic.
3.1 Modification of the local cabinet a. Remove the following components on the local cabinet: High oil level, low alarm, small unit reset, small unit tripping, allowable main valve test, normal high/low pressure main valve test ; Exhaust steam temperature and speed 2 meter; oil level meter test, emergency stop, high pressure main valve and low pressure main valve test 4 buttons; all intermediate relays in the cabinet. The mechanical overspeed trip reset button and six pressure gauges are still left on the floor cabinet, and the mechanical overspeed trip reset button contact signal is sent to the No. 18 DPU.
b. Replace and rearrange the local cabinet terminals.
c. Replace the signal cable from the local device to the local cabinet and the local cabinet to the DCS and TSl cabinets.
3.2 The transformation of the power supply The small cabinet DCll0V and AC220V control power supplies are sent from the power distribution center to the local cabinet. After the modification, cancel the DCllOV and AC220V power supplies from the power distribution center to the in-place cabinet, and increase the power distribution center to the centralized control power cabinet. The DCllOV power supply of the 4JSB cabinet is divided into 5 small switches in the power cabinet to be used as small and high voltages. The main valve opens and closes the solenoid valve and the power of the small trip solenoid valve SVl, SV2. In addition, set up four AC220V small switches as the zero speed switch, small high and low pressure hydrophobic 1 door and small reset solenoid valve SV7A, SV7BE6 source.
3.3 Relay contact transformation The contact of J17 relay cabinet internal relay k78 is changed from the normally open contact to the normally closed contact. The BTG disk emergency trip button retains the original hard-wired circuit and implements the trip function. The original BTG disc emergency trip button controls the k78 relay. The k78 relay normally open contact is sent to the local cabinet relay ESX. The trip relay 86T is controlled by the contact of the relay ESX. When the BTG disk emergency trip button is pressed, the contact point on the button is turned on, 28 is charged, and the normally open contact of the k78 relay is closed to make the relay ESX energized. The ESX normally open contact is closed and the trip relay 86T is energized. The solenoid valve SVl, SV2 loses power and small machine A trips. After the transformation, the k98 relay contact directly enters the tripping solenoid valve SVl, SV2 electrical circuit, when the small machine normal operation, the contact is in the on state, so the contact should be changed to the normally closed contact.
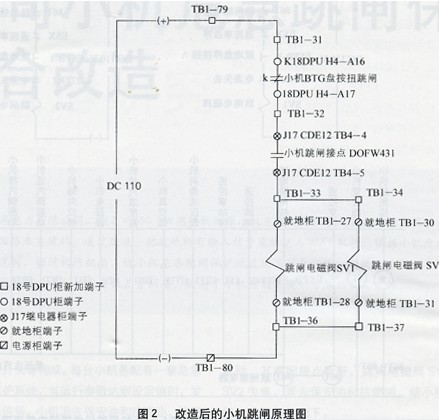
With the contact point, the contact is connected during normal operation. When the "manual stop" button is pressed, the contact is disconnected. The tripping solenoid valve ports SVl and SV2 are de-energized, and the security oil and anti-fuel oil are discharged.
b. The small exhaust steamer valve is not fully protected. The alarm is changed by tripping.
c. Cancel the high/low pressure main valve test control function of on-site cabinet minicomputer, and retain the operator station test function.
d. To cancel the high/low test function of the oil level on the local cabinet, add the high/low alarm on the oil level in the operator station screen.
e. Added a small soft reset function to the operator station.
f. Small machine reset adopts one-button reset, that is, the original BTG disk and local reset to establish trip hydraulic pressure to any reset button to reset can establish trip hydraulic pressure (on-site reset button, BTG disk small hand operator reset Button, operator station soft reset).
g. As all the intermediate relays of the floor cabinet have been removed, the contact originally used by the relay 86T as the reset signal of the small machine and the trip signal no longer exists, and the reset signal and the trip signal are replaced by the security oil pressure signal (63TT) after the modification.
h. In the 18th DPU increase the small machine to reset the Dl point in place.
i. Three screens related to the operator station and the small machine, alarm window prompts, trip condition display, buttons, text, and signal indications are modified accordingly.
Fourth, the transformation effect This transformation eliminates many of the original control system of hidden dangers, and significantly improved the reliability and economic control of the small machine control system.
a. Dismantled all the relays and other electrical components of the local cabinet, and sent the signal directly to the DPU cabinet through the local cabinet, which reduced the intermediate links and made the system more simple and clearer and more intuitive.
b. All signals after transformation can be enforced by point information, and the system is more secure and reliable.
c. The transformation of the power supply system ensures the independence of each user's power supply and ensures the safety and stability of the control system.
d. The modification of the operator station screen allows the operator to see at a glance the operating conditions and the trip conditions of the small machine.
Twin-Wall Pc Hollow Sheet ,Pc Lite Polycarbonate Hollow Sheet,Polycarbonate Hollow Sheet,Hollow Core Polycarbonate Sheets
NINGBO CHAOMEI PLASTIC CO.,LTD , https://www.pcban88.com