Ortrander Eisenhütte, a steel foundry in Dresden, Germany, now uses an RFID system to track forklifts and containers in the plant. When the system is fully implemented, Ortrander Eisenhütte will use ultra-wideband (UWB) active RFID tags to track 20-30 forklifts and passive UHF RFID tags to track 10,000 metal totes and their loads.
Ortrander casts components for the automotive and household industries, with revenues of $30 million last year. During 2001 and 2002, the company invested heavily in expanding production, and its production doubled in 2008. In 2007, the company's management launched a project to upgrade the company's material flow, warehousing and information flow to make these processes more transparent and effective, and to better handle high volume products.
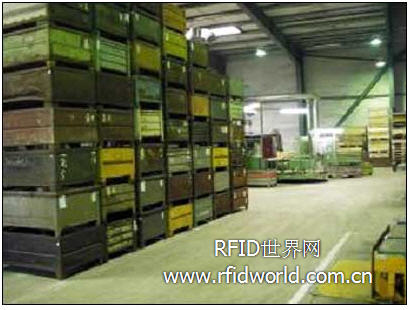
The project includes plans to track forklifts and totes using RFID. Ortrander signed a contract with Fraunhofer Logistics Systems Planning and Information Systems Application Center (Fraunhofer ALI), which helped Ortrander research the market for RFID information management systems, looking for a set of RF that can affect RFID systems in harsh industrial and metal environments Wave) working RFID system.
Ortrander chose Ubisense, a provider of UWB Real Time Location System (RTLS). Ubisense's UWB tag transmits a series of short signals (one hundredth of a billionth of a second or less); the extremely short nature of the pulse wave makes the tag less susceptible to RF noise and interference from metal and other nearby objects. The reader of the RTLS system receives the tag signal through the phase-arranged antenna. The reader uses two complementary techniques to calculate the label position: Time Difference of Arrival (TDOA) and Angle of Arrival (AOA). By adopting this technology at the same time, Ubisense claims that RTLS covers a region with fewer readers than a TDOA-only system.
Ortrander is currently selecting a manufacturer of passive UHF RFID systems, and the details of the specific technology used have not yet been decided. Fraunhofer ALI has developed software to link Ubisense RTLS to Ortrander's ERP system.
In early 2008, Ortrander tested Ubisense's active tags and readers, as well as Euro ID's passive tags and other components. A month later, the company began to implement the program in the factory, focusing on the active RFID part.
The forklift is fitted with two Ubisense tags, one on the roof and the other on the outside of the cab. The tag collects 6-8.5 GHz signals at a frequency of 20 times per second. Due to the large bandwidth of 1.2 GHz, the signal is less disturbed, causing the forklift positioning error to be between +/-15 cm, according to Ubisense sales manager Holger Hartweg.
A total of 11 readers were installed on a 2,500 square meter site (for cleaning cast parts), and a forklift tracking system was implemented in three locations. RTLS captures the signal from the forklift tag and its ID number, and then analyzes the position of the forklift in the warehouse. Since the tag is installed in different parts of the forklift, the system can also determine the running direction of the forklift.
Ortrander is currently installing passive UHF RFID to track the tote, which is expected to be completed by the middle of this year. Ortrander places the totes on pallets and transports them to different locations. A passive RFID tag will be installed at the bottom of each tote. When the totes are filled with cast parts, they are transported to the warehouse and temporarily stacked on the floor or storage rack.
The forklift also installs UHF RFID readers and antennas to identify UHF RFID tags on the container. Ortrander and Fraunhofer ALI are still working on label types and label sets. When the driver picks up a tote, the forklift's reader identifies the box's UHF RFID tag, which system will identify which tote and when it will be moved. This information is then combined with the position information of the forklift to let the manager know which tote was removed.
Currently, Ubisense installs a scale on the forklift to weigh the tote. The system subtracts the weight of the empty container to obtain a negative weight. Since the tote can be loaded with different cast products, these data will help determine the product in the tote.
Ortrander CEO Bernd Williams-Boock says the system helps companies position items faster and increase production visibility. The system is expected to be fully operational in the summer of 2009.
Women Corset ,Limming Sculpting Clothes,Women Sculpting Clothes,Sculpting Clothes
Wenzhou Yingjie Arts and Crafts Co.,LTD , https://www.wzyingjies.com