Cement Grout Plant Description:
The LGP400/700/100PL-D cement grout plant is combination of mixer, agitator and hydraulic plunger grout pump in one plant. Mainly suitable for mixing and pumping water, cement, sand, bentonite, filler, clay power, silicates and other additives.
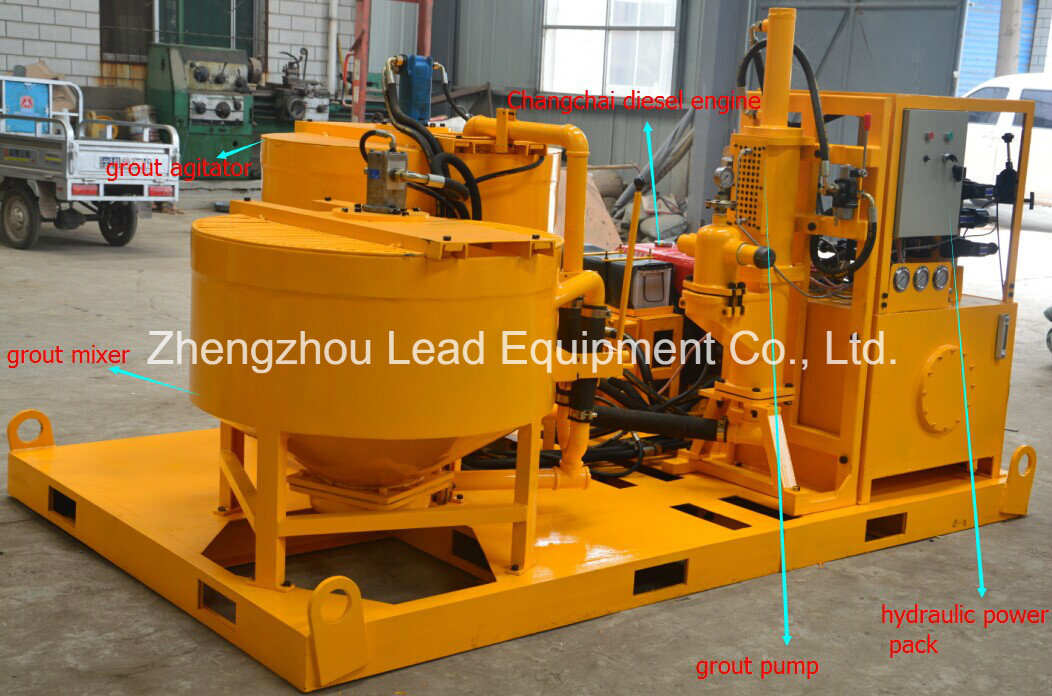
Cement Grout Plant Feature:
1. Compact size, It is combination of mixer, agitator and hydraulic plunger grout pump in one base frame;
2. Have low pressure and high pressure, stepless speed regulation;
3. Yuken relief valve and directional valve for hydraulic system of grout pump;
4. Butterfly valve of mixer and agitator;
5. Oil temperature gauge can automatically control cooler fan working in normal temperature range, if temperature is too high, the machine will stop work automatically;
6. Full hydraulic drive, diesel engine.
7. Operation and maintenance are simple;
8. With ISO, CE certificate.
Â
Cement Grout Plant Applications:
1. Civil Engineering - dam foundations, tunnels, mining, soil nails, tiebacks, earth anchors, cable and rock bolts
2. Structural - building and bridge restoration, foundation stabilization, foundation raising, soil compaction grouting; soil & rock grouting
3. Construction - pavement under sealing, slab jacking and slab raising
4.  Marine - underwater foundations, piers, breakers, shoreline foundations
5.  Mining - tunnel lining, contact grouting, shaft waterproofing
6.  Utilities - encasements, waterproofing, slope line grouting
7.  Geotechnical - deep well casing, monitor wells, well sealing and abandonment.
 Cement Grout Plant Technical data
Type | LGP400/700/100PL-D Grout Plant |
Diesel engine | 25kw/36HP |
Rotating speed of engine | 2200r/min |
Dimensions | 2900*1900*1750mm |
Weight | 1900kg |
                                   Mixer | |
Capacity | 400L |
W/C ratio | 0.5-1 |
Rated Rev. | 1500rpm |
                                             Agitator | |
Volume | 700L |
Rated Rev. | 36rpm |
                                               Pump | |
Type | Hydraulic Plunger pump |
Pressure and Output | Â 25 Bar (low pressure)Â Â Â 100L/min |
50 Bar (high pressure)Â Â 40L/min |
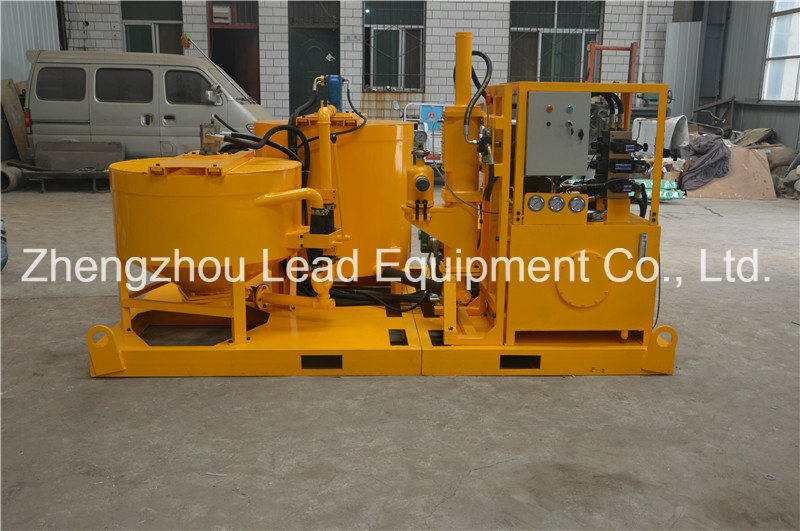
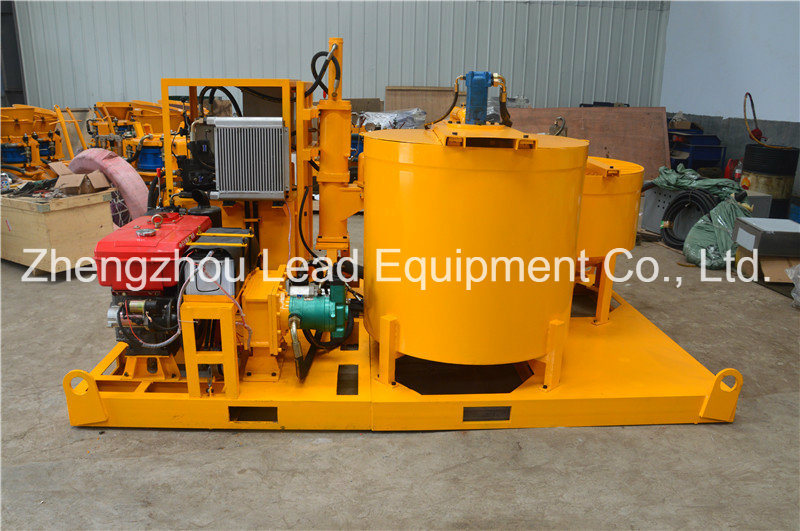
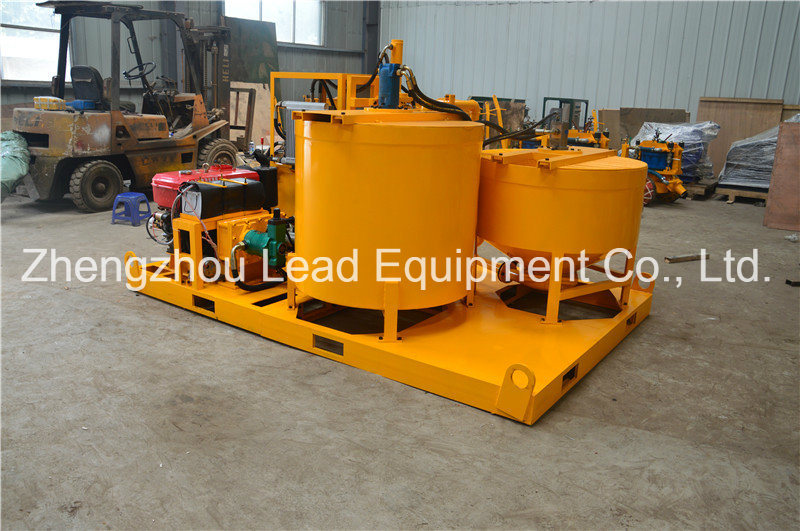
In order to convenient for transpot, the grout station coulde be devide into two parts: grout pump with hydraulic power unit, grout mixer and agitator.
Grout pump with hydraulic power unit
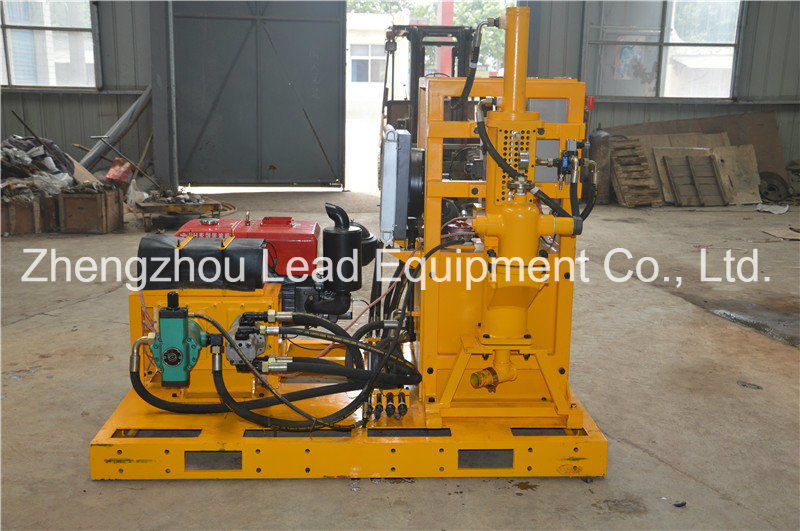
Grout mixer and agitator
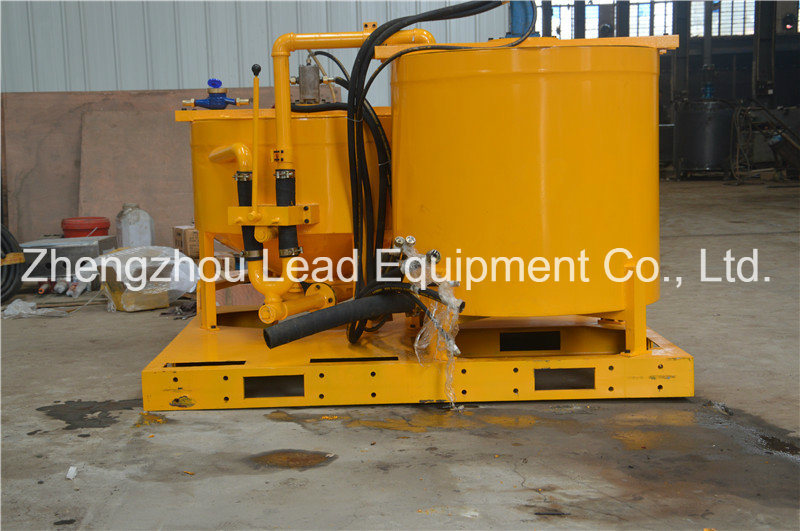
Any question or interested, please contact   or +86-15736772513 for more information now!!!
The hydroforming process has a wide range of applications in the automotive, aerospace, aerospace and pipeline industries. It is mainly suitable for: circular, rectangular or profiled hollow structural members that vary along the axis of the component, such as automotive exhaust system shaped pipe fittings; non-circular cross section Hollow frames, such as engine brackets, instrument panel brackets, body frames (about 11% to 15% of automotive mass); hollow shafts and complex fittings. Figure 2 shows some of the typical parts that the hydroforming process is used in the automotive industry.
Suitable materials for the hydroforming process include carbon steel, stainless steel, aluminum alloy, copper alloy and nickel alloy. In principle, the materials suitable for cold forming are suitable for the hydroforming process. Mainly for auto parts factory, electronics factory, electrical factory, heat treatment factory, vehicle parts factory, gear factory, air conditioning parts factory.
For hollow variable-section structural members, the conventional manufacturing process is to first form two halves of the sheet and then weld them into a whole, and hydroforming can integrally form a hollow structural member that varies along the cross-section of the member at one time. Compared to stamping and welding processes, hydroforming techniques and processes have the following major advantages:
1. Reduce quality and save materials. For typical parts such as automobile engine brackets and radiator brackets, hydroformed parts are 20% to 40% lighter than stamped parts; for hollow stepped shaft parts, 40% to 50% of weight can be reduced.
2. Reduce the number of parts and molds and reduce mold costs. Hydroformed parts usually require only one set of molds, while stampings mostly require multiple sets of molds. The number of hydroformed engine bracket parts has been reduced from 6 to 1, and the number of radiator bracket parts has been reduced from 17 to 10.
3. It can reduce the amount of welding for subsequent machining and assembly. Taking the radiator bracket as an example, the heat dissipation area is increased by 43%, the number of solder joints is reduced from 174 to 20, the number of processes is reduced from 13 to 6 and the productivity is increased by 66%.
4. Improve strength and stiffness, especially fatigue strength, such as hydroformed radiator brackets, which can increase stiffness by 39% in the vertical direction and 50% in the horizontal direction.
5. Reduce production costs. According to the statistical analysis of the applied hydroformed parts, the production cost of the hydroformed parts is reduced by 15%~20% on average, and the mold cost is reduced by 20%~30%.
Hydraulic Press for Head Cover
Hydraulic Press for Head Cover,4 Column Hydraulic Press for Head Cover,Hydraulic Press for Head Cover 200 Ton,Hydraulic Press for Head Cover 400 Ton
CHENGDU ZHENGXI HYDRAULIC EQUIPMENT MANUFACTURING CO., LTD. , http://www.zxhydraulic.com